塑料成型与制造/模具设计
模具设计 是一项复杂的工作,需要考虑许多方面,从产品的形状到冷却系统的细微之处。
一般来说,注塑模具用于大规模生产相当简单的零件和部件,这些零件和部件可以随后组装成复杂的产.品。零件必须相当简单的原因是,它们必须从模具中取出,而模具是在注塑熔融流固化后制成的。
模具的成本通常在几万欧元到几十万欧元之间。
模具的设计和制造时间从几周到几个月不等。
模具种类很多,可以用多种标准进行分类:生产量、脱模系统和方向、流道系统等。
模具的建造需要很高的成本和时间,因此它们通常用于大批量生产(至少几百个或几千个产品)。通常用钢材制造的普通模具用于年产量从 10,000 件到几百万件的零件。
用于小批量生产或试模工具(用于测试成型工艺的可行性和研究其行为)的模具是用易于加工和成本更低的合金(如铝)制造的。
由模具生产的每个零件都必须从模具中取出。因此,零件可以通过自然脱落、顶出和脱落、自动化提取(由外部机器人)、手动取出等方式取出。
此外,注塑机可以是水平的或垂直的,因此模具可以为相应的夹紧系统而设计。
模具可以分为冷流道、热流道或混合流道。
基本的模具机构只包含一块顶出板,它移动顶出杆以取出零件。然而,使用多块移动板来取出带有抽芯的复杂零件非常常见。
材料描述
ABS 常见的热塑性塑料,具有良好的抗冲击性和韧性。聚丙烯 用于多种应用的热塑性聚合物。聚甲醛 尺寸稳定的热塑性塑料,具有高刚度和低摩擦。聚碳酸酯 耐温性和抗冲击性良好的热塑性材料。聚碳酸酯/ABS PC 和 ABS 的混合物,可制造适用于各种应用的坚固零件。PVC PVC 是一种聚合物,具有良好的绝缘性能、高硬度和良好的机械性能。尼龙 耐用的聚合物材料,具有高伸长率和良好的耐磨性。尼龙 32% 玻璃纤维 具有优异的机械强度和高温耐受性的聚合物。丙烯酸(PMMA) 耐破损的材料,常用于透明应用。苯乙烯 轻质材料,以其高抗冲击性和韧性而闻名。聚醚酰亚胺 耐高温且具有优异机械性能的热塑性塑料。
模具中的模腔以多种方式实现,它们必须遵循专门的设计规则,并且可以有各种尺寸和形状。
要进行注塑的零件设计必须符合以下要求
- 必须能够用塑料流体填充零件,即
- 零件必须是连续的固体(否则必须考虑多个注塑点)
- 壁不能太薄
- 流动长度不能太长
- 注塑前模腔中存在的空气必须有排出(见排气)或压缩在不可见区域的可能性
- 流体必须快速冷却并凝固,即
- 热量必须通过冷却系统排出
- 零件不能有非常深和笨重的区域,它们必须被清空,只留下结构肋
- 塑料材料在凝固过程中有明显的体积收缩(约 0.5 - 3.0%),因此模具上的模腔尺寸必须放大,以便在使用温度下完全收缩后,零件尺寸达到所需尺寸。
- 零件必须能够脱模,即
- 零件不能有抽芯(或考虑针对每个抽芯的运动,否则零件必须分开,用多个模具或模腔制造)
- 所有垂直壁上必须存在斜度;它必须指向每个半模的分型线
- 塑料材料,特别是如果是非各向同性的,会导致注塑件的不对称收缩:因此,用预变形形状设计模具是有用的,这样一旦零件完全收缩,最终形状就会对应于所需的形状。
- 一些表面的纹理或粗糙度会在垂直面上产生微小的型芯,导致无法正确脱模和推出。
- 某些表面处理可能需要特殊的模腔材料(例如镜面抛光表面)。
- 如果零件需要在推出后由机器人操作,则零件设计必须考虑真空吸盘或夹具的夹取特征。
模腔通常通过减材制造,使用加工工具实现。然而,许多细节和特殊之处可以通过其他方法或技术来获得。主要使用的技术包括
- 机械加工(铣削,钻孔,[[w:磨削|磨削],抛光)
- 电火花加工(EDM)
- 增材制造
- 电化学加工(ECM)
- 激光雕刻
- 焊接(仅用于修复或修改)
模具制造广泛使用标准化元件,例如结构块、数据时钟、机械传动装置等。
最典型的模具制造流程
- 模具项目实现
- 采购金属块和标准化块
- 金属块粗加工
- 模腔精加工
- 模腔表面处理
- 组装
- 模具测试(干式和安装在注塑机上)
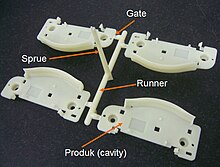
流道系统是连接注塑机喷嘴到将塑化熔料注入型腔的浇口的通道系统。
其组成部分通常称为
- 浇口套(第一个直通道)
- 主流道和副流道(从浇口套开始,然后由主流道开始的分支,适用于多型腔模具或多个注射点)
- 浇口
尽管浇口套仅存在于冷流道系统中,但一些常见元件也存在于热流道系统或混合系统中。
浇口通道由浇口套衬套形成,该衬套将来自压机喷嘴的塑化熔料引导到通道中。通道与喷嘴的密封仅通过接触实现,通过机器施加在料筒上的力实现。为了正确密封接触面,并确保轻松脱模和在整个零件成型完成之前不会发生冻结,通常遵守以下关系[1]
- 喷嘴的球面半径R必须小于或等于浇口套衬套凹槽的半径r(通常比后者小 1 毫米)。
- 喷嘴孔径dN必须小于或等于浇口套衬套入口孔径dD(通常比后者小 1 毫米)。
- 浇口套必须呈锥形,通常建议的锥角为 4 度,至少为 1 度。
- 浇口套衬套的直径必须有限制,以避免由于温度梯度和密封力造成的应力。该部件的温度通常比模具半边高。
市售的浇口套衬套也可用。
在单型腔模具中,浇口套通常与由动模保持的零件一起脱模,而在多型腔模具中,使用浇口拉杆将浇口套固定在动模中。浇口拉杆通常是位于动模中浇口套末端对应位置的短锥形凹槽,与浇口套的锥度一致,起着型芯的作用。[2]
-
Z 形浇口拉杆
-
圆柱形浇口拉杆
-
带槽浇口拉杆
浇口拉杆也可以作为冷料井:一个型腔,用于将热塑化熔料与模具接触时冷凝,而不会被输送到型腔中,从而避免零件表面出现缺陷。
主流道将熔料从浇口套通道输送到浇口,必须满足以下要求:[3]
- 在浇口和零件冷凝后冷凝,因此其厚度应大于零件最厚的壁厚部分(通常建议 D = smax + 1.5 毫米)。
- 路径要短:为了缩短循环时间,延迟冷凝,减少材料浪费和降低压降(通常建议小于 30 兆帕)。
- 通常不进行抛光,以使冷凝的熔料更好地附着在主流道上,而不是流入零件中(除了某些材料,建议进行抛光,例如 PVC、聚碳酸酯和聚甲醛)。
-
U 形或抛物线形主流道截面,非常常见,通常在模具动模一侧形成凹槽,以便轻松推出。
-
梯形主流道截面,由于周长和横截面积较大,会产生更多热交换和废料,通常在模具动模一侧形成凹槽,以便轻松推出。
-
半圆形主流道截面,由于拔模角较小,不太有利于推出。
-
圆形主流道截面,由于拔模角较小,不太有利于推出;更昂贵,浪费时间,需要在模具的两侧都形成凹槽。
冷流道系统生产带有浇口套的零件。多型腔模具需要一个浇口套加一个主流道,如果有必要,还需要一定数量的副流道(如果有多于两个型腔)。对于设计有多个注射点的零件也是如此。
主流道的尺寸设计用于将熔料均匀地分配到所有型腔:由于熔料流动动力学对表面缺陷、非均质塑化熔料特性和其他间接因素的高度敏感性,实现熔料的良好分配是一个艰巨的目标。如果模具生产形状不同的零件,则主流道需要按比例分配熔料流动,而不是均匀分配,以便在相似的时间、压力、速度下填充每个零件所需的体积。
热塑性塑料的浇口套通常可以在研磨后重复使用,在批次结束时或在注塑机旁使用研磨机研磨。浇口套的重复使用,与任何模塑塑料的重复使用一样,会改变并降低塑化熔料的特性,并可能导致注塑零件出现缺陷:因此,为了获得高质量的成果,仅当每批次中重复使用材料的百分比有限制(占总量的 10-20%)时,才允许研磨浇口套。
该系统可以用于热固性材料和热塑性材料。
热流道系统是一种可以提高注塑效率和质量的系统。然而,该系统只能用于热塑性材料,因为浇口套无法在固态下推出(它会再次熔化,用作生产第一批零件的原材料)。
如果经过精细优化,该系统可以更高效,尤其是由于没有浇口套材料浪费,循环时间更短,缺陷零件数量更少。另一方面,该系统需要更高的模具投资和更高的加热热流道所需的能耗。
该系统包括一个模具块,其中包含一个热流道,它可以使熔料在进入模具的第一个区域保持熔化状态。该块由几个板组成,板之间连接在一起,包含将塑化熔料输送到型腔的流道,如有必要,通过喷嘴将熔料分配到多个注射点。在板之间还安装了电阻丝和热电偶,以便加热流道并控制其温度。
需要一个控制器来控制热流道的温度和电阻丝的电流强度。通常,有几个可以单独控制的回路。这种控制使得多型腔或多注射点模具的工艺控制更加容易。通常情况下,对流道区域进行温度控制,并对每个喷嘴进行温度控制:这对于控制多型腔模具每个型腔的熔料流动粘度非常有用,以便将其平衡。
该系统允许不使用浇口,因为它可以保持浇口熔融状态,无需脱模。
但是,含有型腔的模板需要保持比热流道模板更低的温度:这可以通过隔热和冷却来实现。
综述
- 优点
- 无需脱模的浇口
- 提高零件质量
- 提高工艺控制(尤其适用于多型腔或多注射模具)
- 缺点
- 仅限于热塑性材料
- 热流道系统和控制器的投资增加
- 加热塑化材料的能耗增加
- 固定部分热交换隔离和冷却的难度增加
流道的布局取决于几个因素
- 在浇口上均匀分配流速和压力(对于多型腔模具或具有多个注射点的零件)
- 模具的简单制造和设计
- 易于脱模(通过经典的推出或机器人系统)
- 浇口设计
- 使用的流道数量。
一个简单且普遍推荐的布局是拥有 2n 个型腔和“H 形”流道路径,这可以轻松地使型腔和流道均匀分布。在这种情况下,通道截面必须简单地减半以进行每次分叉。这导致了具有 1、2、4、8、16 等型腔的模具。
但是,几个原因可能会支持不同的布局,例如
- 成本和简便性方面的因素可能建议在使用共同运动可以用于多个型腔时采用线性布局,以避免移动部件、执行器和使用空间的倍增
- 需要用所需数量的型腔填充机器的可用空间(即使避免使用奇数个型腔以保持对称性)
流道系统可以包括一些浇口拉拔器或其他几何形状,这些几何形状专门用于通过重力或机器人手臂来实现或帮助浇口的移除:一个例子是用于通过吸盘对浇口和流道进行机器人处理的扁平圆盘。
浇口是材料流的入口,它通常是
- 材料流过的最薄通道(不包括流道-浇口的情况)
- 位于零件的不可见且非功能性或关键点
- 尺寸与以下因素相关
- 零件的最薄壁
- 材料流的特性(粘度、温度、收缩等)
由于浇口导致的流道截面限制会导致其在浇口附近的温度显着升高,这通常有助于填充零件的薄壁并推迟材料在浇口区域的凝固。
由于推出容易或零件的质量,许多可能的浇口配置是可能的。一些可能的浇口设计
- 隧道浇口
- 浇口浇口
- 边浇口
- 径向浇口
- 倒浇口浇口
- 圆形浇口
- 直接/喷嘴浇口
- 关闭喷嘴/阀门浇口
-
浇口浇口
-
边浇口
-
环形浇口
-
倒浇口浇口(针尖浇口)
-
直接热喷嘴
一些浇口配置有助于自动移除浇口,例如隧道浇口,因为脱模零件的小连接点很容易在模具打开或由处理机器人机械地分离。浇口浇口和边浇口通常通过人工或安装在处理机器人上的机械刀分离。浇口拉拔器也可以用来将浇口锁定在移动模具半边的时间比型腔更长,以分离两者。
推出零件是模塑的一个基本步骤,它主要通过以下方式执行
- 机械推出器运动:几乎总是存在于将零件推出型腔
- 吹气:不会对零件造成局部压力,有助于推出大型零件
- 机器人处理:柔和处理,零件不会掉到地上,不会发生变形或表面损伤
- 模具打开运动和重力
零件也可以通过组合上述系统来推出。浇口或不同的零件可以以不同的方式推出:典型的是通过浇口拾取机器人来移除浇口,这样浇口就不会在以后与零件一起选择。